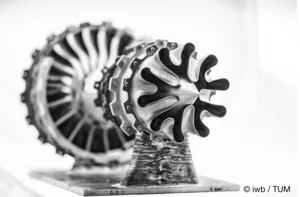
The Department Additive Manufacturing at the iwb concentrates on the processing of metallic materials. The process portfolio includes selective laser beam melting (LBM), wire and arc additive manufacturing (WAAM), binder jetting and ink jet printing. Various systems for processing polymers, which are primarily used for teaching or for the production of prototypes, complete the equipment. The methodological core competencies of the Department Additive Manufacturing include process development, process simulation on different scales and process monitoring. In addition, the Department Additive Manufacturing possesses expertise in the field of machining post-processing of additively manufactured components through joint research work with the Department Machine Tools.

As a participating member of the TUM.Additive Cluster, the Chair of Aerodynamics and Fluid Mechanics is developing advanced numerical simulation methods for predicting the thermo-fluid dynamics in additive manufacturing processes. The aim of our research is to improve process understanding and develop innovative manufacturing technologies through detailed simulations using a virtual twin.
As experts in the field of fluid dynamics, our work focuses on numerical modeling, where we develop efficient methods for calculating complex flow dynamics and heat transfer. Our simulation tools are specifically optimized for high-performance computing on modern computer architectures, enabling high-resolution predictions of the actual physical process behavior. Our goal is to achieve higher accuracy and reproducibility in additive manufacturing through our insights. In our simulations of additive manufacturing processes, we concentrate on quantitative predictions of the interplay between process parameters and flow behavior. By understanding the underlying mechanisms, conclusions can be drawn about the resulting macroscopic properties of the components. We particularly investigate potential sources of defects and propose process optimizations. Our simulation work spans various scales, from crystal growth to melt pool dynamics and shielding gas flow in the build chamber. Our research in additive manufacturing not only enhances the understanding of underlying physical mechanisms but also provides valuable insights for the advancement and application of these promising technologies. We collaborate closely with our industry partners to implement the results of our research into practice as quickly as possible and promote the use of additive manufacturing in various industries.

At the Chair of Plant and Process Engineering, the "downsizing" of distillation columns is currently being investigated on a laboratory scale. The objective is to reduce the column diameter from DN50 to DN20. This reduction is expected to enhance the resource efficiency and sustainable operation of distillation columns on a laboratory scale. The investigation involves the utilization of structured packing, which can be manufactured using 3D printing technology at the laboratory scale. These packings are experimentally and computationally (CFD) tested in a distillation column with a diameter of DN20 to optimize their performance and efficiency.
The use of 3D printing facilitates the realization of complex geometries and surface structures that would be impractical or unfeasible to achieve through conventional manufacturing methods. This opens up new possibilities for the targeted design of packing surfaces, which are essential for mass transfer in distillation processes. In the course of both experimental and simulation-based investigations, various parameters such as separation efficiency, pressure drop, and liquid distribution are examined to optimize the performance of the 3D-printed packings.
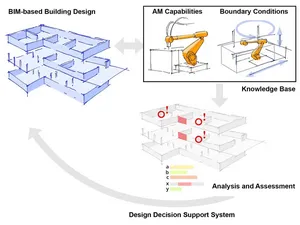
Additive Manufacturing (AM) in construction envisions a possible alternative to predominantly manual construction with various benefits. However, the application of Additive Manufacturing in construction projects has to be carefully evaluated, especially during the early phases of architectural design when important decisions are made. From this point, we devised a design decision support system (DDSS) to identify suitable building components which can be manufactured with specific AM methods. This system is based on a formal knowledge base and interfaces a BIM authoring tool for evaluating AM methods' feasibility with design adaptations.
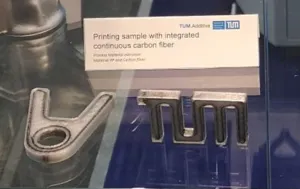
Prof. Klaus Drechsler's Chair of Carbon Composites is conducting research in additive manufacturing technologies that can be used to realize considerable lightweight construction potential - for example, individual fiber composite components in robot-assisted rapid prototyping. For stroke patients a customized exoskeleton of the lower extremities is to be produced in a fully automated process in less than 24 hours.
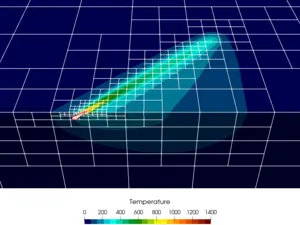
At the Chair of Computing in Civil and Building Engineering (CCBE), we model additive manufacturing processes to gain an insight into the relevant physical mechanisms which govern the process. We also model products of additive manufacturing to develop a qualification system for parts produced by additive manufacturing. Therein, we investigate the structural performance of parts generated by AM using mineral- or metal-based processes. Our methods either start from a CT scan of the finished part or from volumetric models generated online during the production process.
Our process models currently focus on the process of laser powder bed fusion of metals and describe the thermal evolution of the temperature during production at all scales. To address the multi-scale nature of the problem and to be able to compute temperature evolutions at part scale in a feasible amount of computational time, we are developing new methods, such as the space-time finite element method.
The development of efficient methods for the solution of heat evolution also allows us to address inverse problems such as the computation of process parameters to achieve a given melt pool shape or temperature distribution. Inverse problems are currently restricted to patch-scale and thermal problems, yet future work will expand the solution of inverse problems to the scale of the microstructure as well as the part scale.
The Chair of Material Handling, Material Flow, and Logistics (fml) focuses on process and machine development for extrusion-based 3D concrete printing in the field of additive construction, particularly the innovative near-nozzle-mixing method. In addition to research projects, the development of prototypes from design to maintenance represents a central area of responsibility. At the heart of the research is process technology, which encompasses both the optimization and further development of additive manufacturing processes for concrete printing. The expertise of the chair extends to the development of novel processes and the optimization of existing processes for 3D printing of concrete structures. In close cooperation with industry partners and other chairs, the aim is to develop and establish innovative solutions for the use of 3D concrete printing in various application areas.
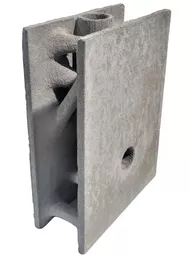
The development of new additive manufacturing processes for applications in construction is one of the research focusses at the Chair of Timber Structures and Building Construction. Different materials (concrete, wood) and processes (extrusion, particle bed) are investigated alternatively and comparatively. In addition, work is being done on standardization and quality assessment in additive manufacturing in construction. Furthermore, the staff of the chair takes care of the management of the AMC-Lab, the research centre for additive manufacturing in construction of the TUM School of Engineering and Design.

The Chair of Machine Elements respectively the Gear Research Center (FZG) investigates additively manufactured machine elements. This currently includes intensive research in the area of cylindrical gears. The investigations focus on load carrying capacity aspects and the behavior in comparison to conventionally manufactured gears, especially also with regard to potentials of lightweight designs, but also the integration of sensors or cooling and lubricating concepts are being considered.
No additive manufacturing systems are operated at the FZG. Due to this, the FZG, with its competence in the design, testing and analysis of gear systems, cooperates with other research institutions with their competence in the production of additively manufactured components.
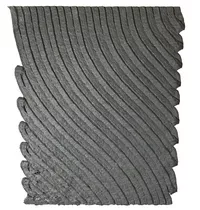
At the Chair of Concrete and Masonry Structures, we study mechanical properties, structural engineering and modelling, reinforcement, as well as large scale behaviour of extrusion 3D printed concrete for application in buildings and infrastructure. Our printing lab is equipped with multiple industrial robots, mixing and pumping equipment suitable for normal and high energy mixtures, as well as advanced sensors to trace the print process in detail and correlate this to mechanical behaviour. Our structural lab allows testing up to the scale of building components and the application of special loading conditions.
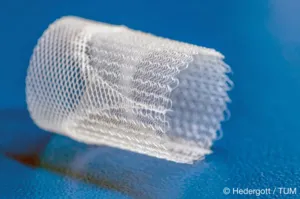
The Chair of Medical Engineering Materials and Implant is working, among other things, on complex, silicone-based structures for the creation of biomimetic organ models. In such model systems, the implants of the future can then be investigated and optimized under physiological conditions before they are used in humans. In addition, research is also being conducted into microstructured topology architectures by means of which the responses of human cells to different cultivation conditions can be studied, such as a biomimetic heart valve. The additive manufacturing process Melt Electrowriting is used here.
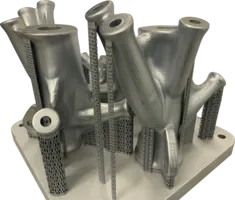
The Chair of Metal Construction is working on the acquisition and evaluation of the decisive influencing factors on the production of safe and durable structural steel elements by laser beam melting of metals (PBF-LB/M). In particular, the relationship and dependencies between PBF-LB/M process, post-treatment and geometry with microstructure and mechanical properties are investigated and modeled. Special focus is on the fatigue of PBF-LB/M-produced austenitic steels - the defects resulting from the manufacturing process (high surface roughness, porosity, special microstructure) are analyzed in detail by the Chair of Metal Engineering with respect to fatigue.
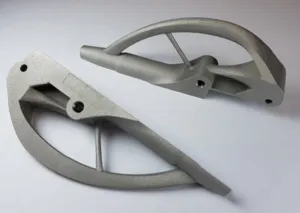
The Chair for Product Development and Lightweight Design covers the design and optimization of technical systems and components, including those that are additively manufactured. This includes simulation and optimization methods, such as topology optimization, as well as Design for Additive Manufacturing (DfAM). Both, the geometrical degrees of freedom that can be used via AM, and the AM-specific constraints are integrated into an overall development context in order to enable lightweight design at the limit of the technically feasible.

With the binder jetting process (powder binder process), additive manufacturing is to be used as a highly innovative tool for the production of molded bodies for heterogeneous catalysis. In this way, shaping possibilities can be opened up which are not possible with any previously established technology and which can enable more efficient, resource-saving and cost-saving catalytic processes. In addition, this also offers the potential to create the scientific and technical prerequisites for the realization of new catalytic routes.
Research in the Chair of Thermodynamics is focused on the fundamental understanding of flow, heat, and chemical reactions across different materials scales with applications in energy, aerospace, process engineering, and beyond. Cross-disciplinary research is the heart of the Institute.
With great historical accumulation and state-of-art computational and experimental facilities, supported by multiscale simulation and experimentation, our expertise in
- Multiphase flow and heat transfer
- Multiscale modelling and simulation
- Combustion and reaction kinetics
- Renewable and solar energy technologies
- Nanomaterials design and nanoengineering
- 3D printing of nanostructures and surfaces
We are developing advanced technologies to tackle problems in energy, power, water, manufacturing, aerospace, and beyond.

At the Chair of Metal Forming and Casting (utg), the droplet-based additive manufacturing of metal components, Material Jetting (MJT), is being investigated and further developed. The semi-finished material for this process is wire-shaped and thus both inexpensive and easy to handle. In the MJT print head, the semi-finished material is melted by resistance heaters and then applied dropwise to a build platform via a nozzle. An MJT test facility is located at utg, which can be used to operate various print heads. Several publicly funded research projects have developed and investigated printheads for aluminum alloys, copper alloys and salts. Current research areas are the processing of copper, the implementation of support structures and the numerical simulation of the process. For the process analysis, high-speed cameras, strength investigations, metallography, contact angle investigations, laser flash analyses and dynamic differential calorimetry are used, among others.
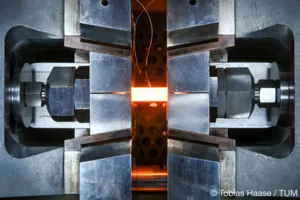
The core of research at the Chair of Materials Engineering for Additive Manufacturing is the analysis of process-structure-property relationships in the additive manufacturing of metallic materials and the use of these findings to develop new materials and processing methods. The focus is on high-performance materials such as high-strength aluminum alloys and alloys for high-temperature applications, as well as multi-material components, graded material structures and metal-matrix composites. While materials engineering issues cover all additive manufacturing processes, process engineering research focuses on direct energy deposition processes (laser and plasma powder cladding as well as wire arc additive manufacturing) and joining of additively manufactured components. Cross-scale material simulation, excellent characterization methods, innovative measurement and testing technology, and state-of-the-art AI-supported data analysis are available to deliver tailored material solutions for the most demanding applications.
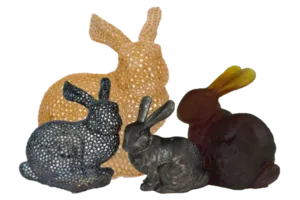
At the Institute of Material Science, we work on additive manufacturing of photopolymeric materials that we convert to metals and carbon through a post process heat treatment. The achievable resolution of patterned features thereby spans from 100 nm up to the cm scale within the one part. We focus on the development of tough, highly temperature stable and biocompatible polymer systems and utilize hot lithography which is unique in that it can process photopolymers at temperatures as high as 120°C. The high temperature enables a wide range of materials and fillers to be processed offering great flexibility and performance not achievable at room temperature. Our current applicational focus lies on carbon electrodes for electrochemical devices such as fuel cells and flow batteries but we are always open to interesting challenges in other fields, where our material systems and competences can be of use. Recently, we started looking at the patterning and sintering of metals and the aforementioned scales, a research direction that is still in its infancy.
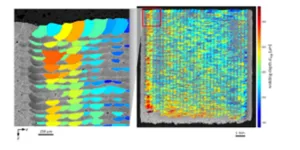
At the Chair of Nondestructive Testing, research is conducted on the application of nondestructive testing in additive manufacturing. The aim is to identify material inhomogeneities such as cracks, pores or changes in the microstructure. A computed tomography system is available for this purpose, with which pores can be detected very precisely. In addition, differences in material properties can also be detected with the help of the chair's ultrasonic measurements. The chair has also built up expertise in acoustic emission analysis. This can be used to detect irregularities already during the process.
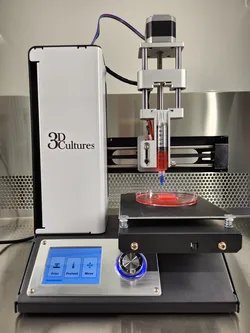
Bioprinting of support structures (scaffolds) is an important technology for exploring the production of cultured meat, i.e. meat grown from animal cells and not derived from slaughter of farm animals. Bioscaffolds can be used to support the growth and development of animal cells and enable the production of cultured meat in a controlled environment. Bioprinting enables precise placement of animal cells and biomaterials so that complex and customized bioscaffolds can be created that mimic the structure of natural meat tissue on a small scale. Furthermore, the Professorship of Cellular Agriculture is using the FDM process to fabricate perfusion bioreactor modules that continuously supply nutrients and oxygen to animal cells, enabling better cell growth and tissue development. This technology is promising for the future of cultured meat research as it has the potential to map flexible scale-down models of perfusion tissue reactors.
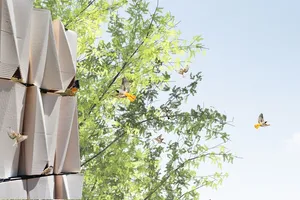
The professorship examines the architectural implications of mobile robotics for additive manufacturin (AM) in construction and develops methods for their implementation. The material deposition method of concrete extrusion is used to investigate mobile part-based AM strategies to produce large objects whose size exceeds the static workspace of the robot. By implementing advanced sensor and control solutions, autonomous localization and precise manipulation techniques for mobile AM are explored. In addition, this research aims to provide scalability to AM processes by examining the use of cooperative robots to collaborate on single fabrication jobs. The ultimate aim of this research is to develop mobile AM technology for its direct implementation on construction sites. Another project is to create digital planning tools for the creation of location-specific façade redesigns that can host cavity-dependent animal species and realize it with AM.

The Professorship of Laser-based Additive Manufacturing covers a wide range of topics along the entire process chain of the manufacturing of plastics, metals and hybrid materials with laser-based additive Manufacturing processes: From material development to novel process strategies, all the way up to automation solutions and quality control. This holistic approach will help to implement innovative technologies in the industrial environment. The research areas of the Professorship are divided into five areas: Innovative process strategies for laser-based powder bed fusion of metals (PBF-LB/M), Quality Assurance in laser-based powder bed fusion with plastics (PBF-LB/P), Hybrid Additive Manufacturing, Laser-Material-Interaction, and Process Monitoring in laser-based powder bed fusion with metal (PBF-LB/M).

The Microrobotic Bioengineering Lab (MRBL) uses microfluidic processes for the production of microrobots for cell research. Nanomaterials and fluorescent sensors are incorporated into hydrogels. This ensures biocompatibility and makes it possible to stimulate and measure individual cells in different ways. Research goals are the production of different microrobots, which are used in the field of mechanical biology and thermal biology.
The chair's expertise is the production of millions of homogeneous microrobots using microfluidics. Depending on the task, the microrobots are functionalized differently and are used in stem cell research, cancer research and the production of tissue structures.
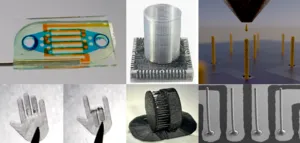
In the Neuroelectronics Group, we explore a diverse array of additive manufacturing techniques to create cutting-edge bioelectronic interfaces and devices, spanning the full spectrum from material formulation to innovative fabrication approaches and device optimization. Our research efforts are focused on developing tailored solutions for advanced neural interfacing technologies. Inkjet printing, a precise droplet-based technique, facilitates the production of conductive tracks and pillar-like 3D electrodes on microelectrode arrays (MEAs) using conductive nanoparticle inks alongside non-conductive passivation inks, with these MEAs engineered to capture electrical signals from 3D cell clusters, such as cortical organoids, in vitro. Stereolithography, a high-precision photopolymerization method, enables the creation of structures with customizable properties based on the chosen materials, where we formulate acrylate-based resins for robust, transparent microfluidic devices and employ water-swellable hydrogels to craft foldable 4D-printed structures for neural interfaces. Filament printing, or Fused Deposition Modeling (FDM), leverages thermoplastic materials for rapid and efficient fabrication, and by optimizing printing parameters and integrating conductive and passivating materials, this approach enables the production of dry electrodes for EEG measurements or fully integrated 3D MEAs within a single printing process. Website
Fungi play a crucial role as destructors in our environment and, at the same time, make an indispensable contribution as symbionts to the healthy growth of almost all terrestrial plants. In our professorship, we study biochemical and molecular genetic mechanisms used by fungi in the recognition, transformation and degradation of wood and other lignocelluloses. In addition, we isolate and characterize plant beneficial fungi and other microorganisms that have positive effects on, for example, plant growth under drought stress, and study fungal-plant communication in the rhizosphere.
In parallel, we are also characterizing the process of colonization and overgrowth of wood and other lignocellulosic substrates by fungi at the morphological and biochemical levels. With the knowledge gained, we are developing new fungal-based composite materials that represent an attractive alternative to petroleum-based materials because they are biodegradable and sustainable. In addition to their use as packaging or insulation materials, we are also looking into the application of fungi in additive manufacturing, such as 3D printing.
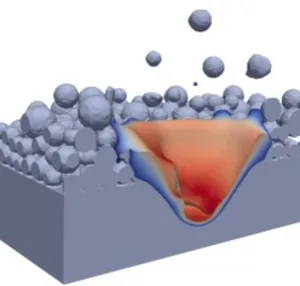
At the Professorship of Simulation for Additive Manufacturing (SAM) the following research in the field of additive manufacturing (AM) takes place. By modeling the different length scales governing AM processes, we aim to gain fundamental understanding of the underlying physics and, eventually, to inspire new process strategies overcoming the short comings of existing processes. In particular, our overall approach considers the modeling of metal powders and powder spreading processes, meltpool modeling, part-scale modeling and microstructure modeling in metal additive manufacturing. While the main focus lies on laser-based powder bed fusion of metals, many of the developed modeling and simulation approaches can be transferred to other AM processes such as Binder Jetting, Directed Energy Deposition and Material Jetting.
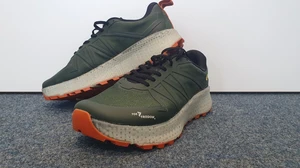
The Associate Professorship of Sport Equipment and Sport Materials uses additive manufacturing processes to develop innovative, customizable sports products. The focus lies on tailored solutions – from cycling shorts and running shoes to orthotics and insoles. In addition, the Chair conducts research on skin-compatible biomaterials to further enhance the comfort and tolerability of individually manufactured products.